توليد سيستم مولتیمديای خودرو
روند توليد محصول در اين شرکت شامل مراحل مختلفي ميباشد که هر مرحله از توليد در يک واحد جداگانه صورت ميپذيرد. مهمترين اين واحدها به شرح ذيل ميباشد:
واحد SMT
در بحث توليد تجهيزات الکترونيکي، اصليترين و مهمترين بخش، برد آن ميباشد، از اين رو در جهت توليد داخلي بردهاي الکترونيکي مورد نياز اين شرکت، واحد SMT در اين مجموعه راه اندازي گرديده است. SMT در واقع تکنولوژي مونتاژ قطعات SMD ميباشد، يعني قطعاتي که روي برد به صورت پايه بلند ميباشند، از روي برد خارج شده و قطعات بسيار کوچکتر به جاي آنها روي برد قرار ميگيرند. بطور مثال، با تکنولوژي قطعات SMD، تجهيزات الکترونيکي موجود در بازار از جمله تلويزيونها، تلفنهاي همراه و … بسيار کوچکتر و باريکتر شدهاند.
خط SMT سه بخش اصلي دارد.
1- Printer
2- Pick & Place
3- Oven
تجهيزات فوق در اين شرکت به صورت Full Inline ميباشند و به يکديگر مرتبط و هوشمند هستند.
دستگاه اول پرینتر
به کمک اين دستگاه قلع مورد نياز بر روي برد الکترونيکي پرينت ميشود، قابل توجه است که دستگاه مورد نظر داراي بازرسي ميباشد، بدين معني که دستگاه قادر است خود را بازرسي نموده و از اين جهت که ضخامت قلع تمام نواحي برد، کم و زياد نباشد و در تمام بخشهاي برد، توزيع به صورت يکنواخت صورت گرفته باشد، مورد سنجش قرار ميدهد، همچنين براي توليدات انبوه بطور مثال 1000 عدد برد، توزيع قلع نسبت به برد اوليه يکسان باشد. دقت اين دستگاه در ابعاد ميکرون (10 به توان 6- متر) ميباشد.
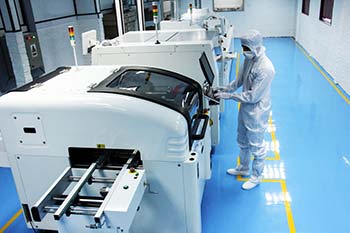
دستگاه دوم Pick & Place:
اين دستگاه داراي يک بازو ميباشد که در سر اين بازو 6 نازل وجود دارد، يعني همزمان ميتواند از دو طرف شش قطعه را به صورت همزمان بلند و جايگذاري کند، سرعت اين دستگاه 28 هزار قطعه در ساعت ميباشد، هر نازل يک دوربين دارد، دوربينها نازلها را قسمت به قسمت و از جمله برداشتن قطعه و صاف بودن آن بررسي ميکنند.
همچنين در اين دستگاه دوربين ثابت قادر است تغذيهکنندهها را از نظر خالي نبودن و درستي انجام کار، به سمت جلو حرکت کردن و همچنين صحت جايگذاري قطعهها بررسي نمايد، اين موارد توسط خود دستگاه به صورت اتوماتيک بررسي ميگردد، بنابراين دستگاه، هوشمند و انعطاف پذير ميباشد، همچنين اين دستگاه قابليت مونتاژ قطعاتي از سايز 0201 به بالا را دارا ميباشد.
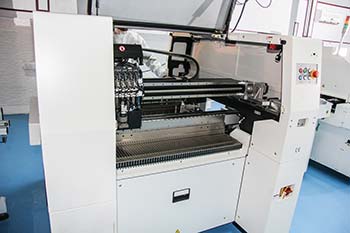
دستگاه سوم Oven:
پس از اينکه قطعات روي قلع قرار گرفتند، بايد در جاي خود ثابت گردند، اين کار توسط Oven انجام ميگيرد، عملکرد آن مانند مايکروويو ميباشد و قطعات را بر روي قلع مقاوم مينمايد.
سالني که توضيح داده شد، به طور کامل بردهاي الکترونيکي سيستم مولتيمديا را توليد مينمايد، اين دستگاه قادر است نقشه هر بردي که به آن داده شود را توليد نمايد، بردهايي که در خودرو استفاده ميشود معمولاً بردهاي چهارلايه و دو رو هستند.
از بين المانهايي که بر روي برد الکترونيکي مونتاژ ميگردند، هميشه تعدادي قطعه هستند که هنوز تکنولوژي SMT قادر به مونتاژ آنها نميباشد، اين قطعات که به صورت پايه بلند ميباشند Dip نام دارند و مونتاژ آنها در واحد Dip صورت ميگيرد.
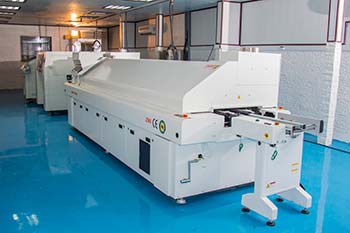
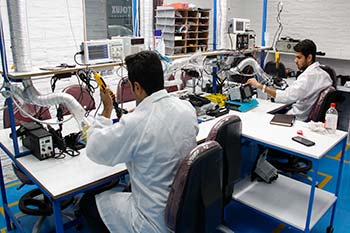
واحد Dip
واحد بعدي، واحد مونتاژ قطعات Dip ميباشد. در اين واحد قطعات باقي مانده به صورت دستي بر روي برد مونتاژ ميشوند و برد در اين مرحله تکميل ميگردد، در نهايت در همان واحد Dip قسمتي براي آزمايش بردها از جهت روشن شدن و تست نهايي برد تعبيه شده است، در صورت عدم وجود مشکل خاص، برد مورد نظر وارد واحد خط توليد مجموعه ميشود.
واحد مونتاژ و توليد
بردهاي توليدي در واحد SMT در مرحلهي بعد وارد سالن مونتاژ ميشوند، مونتاژ به صورت دستي ميباشد و متناسب با نوع محصول توليدي فعاليت انجام شده در هر ايستگاه متفاوت ميباشد، ولي معمولا روند توليد بدين صورت است که در ابتدا برد اصلي به متال زير متصل ميگردد و در ادامه متالهاي چپ و راست و همچنين متال پشت کيس به وسيلهي پيچهاي مخصوص به دستگاه متصل ميگردند. در ايستگاه بعدي از خط توليد معمولا درايور دستگاه متصل ميشود و متال بالاي دستگاه در جاي خود قرار ميگيرد، در ايستگاههاي بعدي پنل السيدي و کيس به وسيله فلتها به يکديگر مرتبط و متصل ميشوند، روند خط توليد با مونتاژ براکتهاي دستگاه (نگه دارندهها) بر روي آن در انتهاي خط مونتاژ پايان ميپذيرد.
واحد QC
مراحل کنترل کیفیت محصولات در خط تولید کارخانه
همهي محصولات توليدي وارد واحد QC ميشوند. اين واحد شامل ايستگاههاي مختلفي ميباشد.
ایستگاه اول QC: آزمون GPS و رادیو
در اوليـن ايستگـاه کنتـرل کيفيـت، آنتندهي GPS مورد بررسـي قــرار ميگيــرد و همچنيــن سـامــانــه Navigation (رهيـاب) موجـود بر روي سيستــم مولتيمدياي توليـدي شرکت، با شبيـهســازي مسيـر حرکت مورد سنجش قرار ميگيرد. در اين ايستگاه، راديوي دستگاه نيز به وسيلهي دستگاه مخصوص تست امواج راديويي تست ميشود، بدين صورت که فرکانس روي دستگاه با فرکانس سيستم مولتيمدياي مورد نظر تنظيم ميشود و سپس امواج فرکانس مورد نظر بررسي ميشود، همچنين به کمک اين دستگاه امکان بررسي خروجيهاي صدا در 4 باند وجود دارد.
ایستگاه دوم تا چهارم QC: آزمون درایور
در سـه ايستگـاه بعد با توجه به اهميت درايــور دستگــاه، آزمــون درايــور با حداقـل 2 عـدد CD و DVD به دقت بررسي ميشود. از موارد ديگر، بررسي خواندن کارت حافظهي موزيک (Music SD) و اجـراي فـايلهـاي بعـدي و يا قبـلي به سـه روش (دکمههـاي لمسـي، دکمههاي پنل و دکمهي ولوم) ميباشد.
ایستگاه پنجم: آزمون USB و کنترل فرمان
در اين ايستگاه ابتدا اجراي فايلها از روي USB بررسي ميشود سپــس دکمـــههـــاي دستگاه کنترل فرمان با دکمههــاي دستگــاه مولتيمديـاي توليـدي تنظيم ميشوند.
ایستگاه ششم: آزمون بلوتوث
در انتهــاي خـط، پس از بـررسـي بـلوتـوث دستگــاه که شـامـل امکان برقراري تماس به کمــک بـلوتـوث و همچنيـن صحــت عملکـرد ميکـروفون دستگــاه ميبـاشـد، مراحل کنترل کيفيت خاتمه مييابد.
در همه ايستگاههاي کنترل کيفيت، تست کليدخوري و ACC و ريستکردن دستگاه صورت ميگيرد، همچنين شکل ظاهري محصول توليدي از جمله عدم وجود خطوخش و صحت پيچها مورد بررسي قرار ميگيرد.
اتاق طول عمر:
پس از اتمام مراحل کنترل کيفيت، همهي محصولات جهت بررسي کارکرد واقعي در مدت زمان طولاني وارد اين واحد ميشوند، در اين واحد محصولات بين 4 تا 8 ساعت در حالت جريانکشي روشن ميمانند، زماني که يک سيستم مولتيمدياي خودرو روشن است معمولا در حدود 7/0آمپر جريان ميکشد، اما وقتي دستگاه مورد نظر به چهار عدد بلندگوي روشن متصل است و نيز صدا زياد ميشود اين مقدار به 5 الي 6 آمپر ميرسد، بدين منظور از قطعاتي جهت تست و شبيهسازي بلندگوها استفاده ميشود تا جريان بيشتري از دستگاه کشيده شود و دماي دستگاه افزايش پيدا کند، در تمام اين مدت تمام دستگاههاي موجود در اين واحد به دقت مانيتور ميشوند و در صورت عدم وجود مشکل وارد واحد بستهبندي و ليبلزني ميشوند. در اين واحد بارکد و ليبلهاي مورد نظر بر روي محصول نصب ميشود و محصول مورد نظر به همراه متعلقات آن (دفترچه راهنما، کارت گارانتي، لوح آموزشي، SD نقشه، دسته سيمها و …) بستهبندي ميشوند.
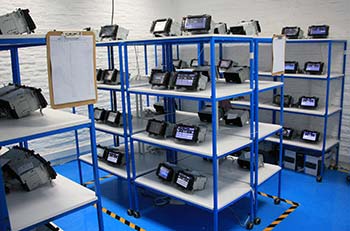
واحد تست های شبيه سازی
واحد ديگر اين مجموعه، واحد تستهاي شبيهسازي جهت ايجاد ضمانت بر روي محصولات توليدي ميباشد، بدين صورت که نمونههاي تصادفي از محصولات توليدي، از فرآيند خط توليد جدا شده و وارد اين واحد ميشوند. اين واحد به مجهزترين و بهروزترين دستگاههاي تست آزمايشگاهي تجهيز شده است و تمامي آزمونها بر اساس استانداردهاي بينالمللي و يا استانداردهاي داخلي بر روي محصولات صورت ميگيرد. بعد از آزمونهايي که در اين واحد صورت ميپذيرد، مجددا کليهي مراحل کنترل کيفيت بر روي نمونهي مورد نظر صورت ميپذيرد.
مهمترين اين آزمونها به شرح زير ميباشند:
تست دما و رطوبت (High Temperature & Humidity chamber):
در اين آزمون تاثيرات دما و رطوبت بر روي ظاهر و کارکرد محصول توليدي مورد بررسي قرار ميگيرد. بدين منظور نمونهي مورد نظر در حالت روشن در داخل محفظهي دستگاه تست قرار ميگيرد. شرايط آزمون از جمله دما و رطوبت بر اساس استاندارد مورد نياز و يا درخواست شرکت خريداري کنندهي محصول تنظيم ميشود. مدت اين آزمون معمولا 8 ساعت ميباشد و تغييرات دماي داخل محفظهي دستگاه تست بر واحد زمان مشابه و يا سخت گيرانهتر از شرايطي است که محصول مورد نظر در يک وضعيت اقليمي گرم و مرطوب در طول يک روز ممکن است تجربه کند. در تمام مدت آزمون نمونهي مورد نظر مورد بررسي قرار ميگيرد و هر گونه تغيير در ظاهر و عملکرد دستگاه به دقت رصد و ثبت ميشود.
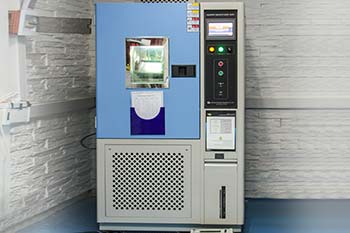
تست شوک حرارتی (Thermal Shock):
تاثیرات دما بر روی کارکرد محصول میتواند مهم و قابل توجه باشد، زمانی که این عامل با فاکتور زمان ترکیب میشود، اهمیت آن دوچندان میشود، بدین معنی که تغییرات دمایی در یک بازه زمانی کوتاه بسیار اهمیت دارد، زیرا ممکن است بر کارکرد واقعی سیستم تاثیرگذار باشد. مشابه این حالت از آزمون در شرایط واقعی کارکرد نیز میتواند کاملا ملموس و قابل دسترس باشد، بطور نمونه، زمانی که محصول مورد نظر در اتومبیلی قرار گرفته است که تحت تاثیر تابش آفتاب در فصل گرم سال قرار دارد و بلافاصله از سیستم خنک کنندهی اتومبیل استفاده میشود، محصول مورد نظر دچار شوک حرارتی میشود، بدین منظور سیکلهای متوالی از شوک حرارتی در بازهی دمایی بالا و پایین بر روی محصول تولیدی در دستگاه آزمون شوک حرارتی اعمال میشود. پس از پایان آزمون فرآیندهای کنترل کیفیت بر روی نمونهی مورد نظر صورت میپذیرد.
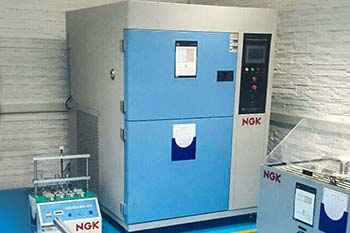
تست گرد و غبار (Dust Test):
تاثیرات دما بر روی کارکرد محصول میتواند مهم و قابل توجه باشد، زمانی که این عامل با فاکتور زمان ترکیب میشود، اهمیت آن دوچندان میشود، بدین معنی که تغییرات دمایی در یک بازه زمانی کوتاه بسیار اهمیت دارد، زیرا ممکن است بر کارکرد واقعی سیستم تاثیرگذار باشد. مشابه این حالت از آزمون در شرایط واقعی کارکرد نیز میتواند کاملا ملموس و قابل دسترس باشد، بطور نمونه، زمانی که محصول مورد نظر در اتومبیلی قرار گرفته است که تحت تاثیر تابش آفتاب در فصل گرم سال قرار دارد و بلافاصله از سیستم خنک کنندهی اتومبیل استفاده میشود، محصول مورد نظر دچار شوک حرارتی میشود، بدین منظور سیکلهای متوالی از شوک حرارتی در بازهی دمایی بالا و پایین بر روی محصول تولیدی در دستگاه آزمون شوک حرارتی اعمال میشود. پس از پایان آزمون فرآیندهای کنترل کیفیت بر روی نمونهی مورد نظر صورت میپذیرد.

تست خوردگی (Salt Spray Test):
جهت بررسی خوردگی سطوح فلزی محصول تولیدی در اثر قرار گرفتن در شرایط مرطوب، این آزمون صورت میپذیرد. در این آزمون محلول سدیم کلرید 95 درصد استفاده میشود و نتایج به صورت درصد خوردگی سطوح اعلام میشود. مدت این آزمون از 24 ساعت تا 240 ساعت متغیر میباشد.
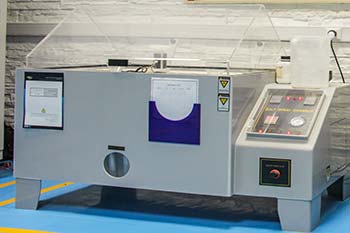
تست کلید زنی (Key Life Test):
با توجـه به گـارانتی تعویـض محصولات تولیـدی شرکت به مدت 2 سال، لازم است که عملکـرد قسمتهای پرکاربرد دستگاه از جمله کلیدهای آن در تعداد دفعات استفادهی مکرر مورد مطالعه و بررسی قرار گیرد، بدین منظور از یک دستگاه کلید زنی پیشرفته استفاده میشود. مکانیزم این دستگاه به صورت مکانیزم سیلندر پیستون عمل میکند و تعداد دفعات کلیدزنی معمولا بین 20 هزار الی 50 هزار بار بسته به نوع کلید مورد نظر انتخاب میشود.
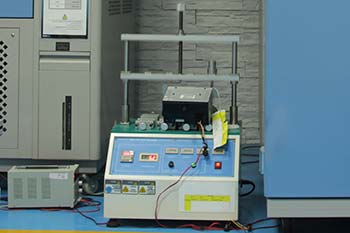
تست ارتعاشات (Vibration Test):
ارتعاشات مکانیکی ممکن است باعث بروز مشکلاتی در محصول شود، لذا با شبیهسازی این ارتعاشات میتوان تاثیرات آن را بر روی عملکرد محصول تولیدی مورد ارزیابی قرار داد، بدین منظور نمونهی مورد نظر ابتدا بر روی میز دستگاه تست ارتعاشات در بین فکهای دستگاه ثابت میشود، سپس با محاسبه و انتخاب فرکانس مورد نظر بسته به نوع استاندارد و مرجع انتخابی برای آزمون، ارتعاشات در راستای 3 محور X,Y,Z به محصول مورد نظر اعمال میشود، بعد از پایان آزمون نیز مجددا مراحل کنترل کیفیت بر روی نمونهی مورد نظر صورت میپذیرد.
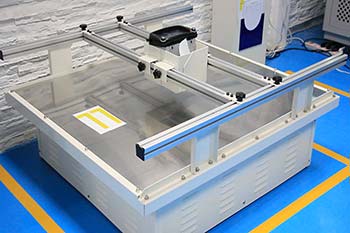
تست گان الکترواستاتیک:
جهت بررسی مقاومت صفحه نمایش محصول تولیدی در مقابل الکتریسیته ی ساکن که ممکن است تحت شرایط خاص از بدن انسان به نمایشگر دستگاه منتقل شود، تست الکترواستاتیک انجام می شود، بدین صورت که با اعمال شوک الکتریکی به نمایشگر دستگاه، خراب شدن احتمالی نمایشگر مورد بررسی قرار می گیرد
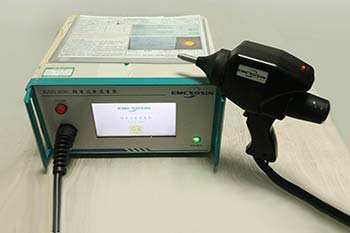